The Comprehensive Guide to Plastic Mold Makers
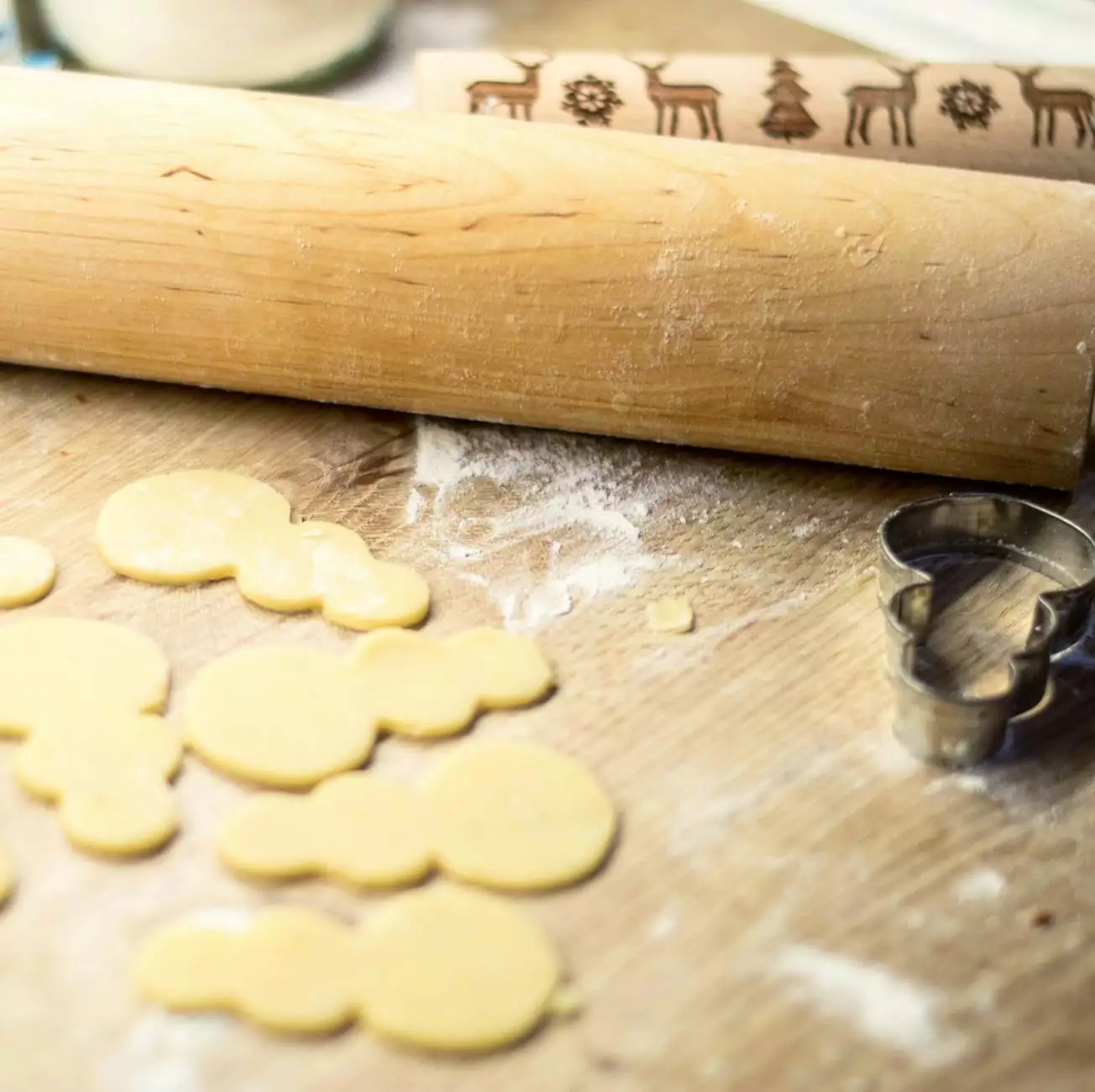
Plastic mold makers play a critical role in the manufacturing landscape, transforming innovative designs into tangible products. Their artistry and engineering prowess shape countless items that are integral to our daily lives. In this extensive article, we will explore the significance of plastic mold makers, the intricacies of their craft, and their influence on various industries.
What are Plastic Mold Makers?
At their core, plastic mold makers are skilled professionals dedicated to designing and creating molds that are used in the injection molding process. This complex manufacturing method involves injecting molten plastic into precisely engineered molds to produce high-quality parts and products.
The Role of Plastic Mold Makers in Manufacturing
Plastic mold makers are essential in multiple sectors, such as:
- Automotive Industry: Manufacturing intricate components like dashboards, bumpers, and other vital parts.
- Consumer Goods: Creating everything from toys to kitchenware.
- Healthcare: Producing medical devices and equipment that require strict compliance with safety standards.
- Electronics: Crafting enclosures and protective casings for a wide range of devices.
Understanding the Process of Plastic Mold Making
The process of creating molds involves several steps, each requiring precision and expertise:
1. Design Phase
The journey begins with an idea. Designers and engineers collaborate to develop a 3D model of the product using Computer-Aided Design (CAD) software. A well-thought-out design is crucial as it influences the flow of plastic, cooling time, and the final quality of the product.
2. Material Selection
Choosing the right material for the mold is vital. Common materials include:
- Steel: Known for its durability, steel molds are ideal for high-production runs.
- Aluminum: Lighter and less expensive, aluminum molds are suitable for shorter production runs.
- Composite Materials: Used for specific applications where both weight reduction and strength are required.
3. Machining Process
Once the design and materials are finalized, the actual mold making begins. Various machines, such as CNC (computer numerical control) mills, lathes, and EDM (electrical discharge machining) equipment, are utilized to achieve the desired shape and precision.
4. Assembly and Testing
After machining, the mold components are assembled. Rigorous testing follows to ensure that the mold accurately produces the intended product without defects. Adjustments are made as needed to perfect the mold's design.
The Importance of Quality in Plastic Mold Making
Quality control is paramount in the mold-making industry. The accuracy of molds directly affects the print quality of every item produced. Therefore, practices such as:
- Material Inspection: Ensuring raw materials meet strict standards.
- Mold Flow Analysis: Using software to simulate and optimize the injection molding process.
- Dimensional Verification: Checking the dimensions of the mold and the produced items.
are routinely performed.
Challenges Faced by Plastic Mold Makers
Despite their expertise, plastic mold makers encounter various challenges, including:
- Rising Material Costs: Fluctuations in the prices of raw materials can impact production budgets.
- Technological Advancements: Keeping up with rapid changes in technology and techniques.
- Environmental Regulations: Adhering to increasingly strict environmental laws and sustainability practices.
Technological Innovations in Mold Making
As industries evolve, so do mold-making technologies. Some of the latest advancements include:
1. 3D Printing
Utilizing 3D printing technology allows for the rapid production of prototypes and even molds. This method significantly reduces production time and costs, enabling designers to iterate their ideas quickly.
2. Advanced Simulation Software
Simulation software aids in predicting how molten plastic will flow within the mold, enabling manufacturers to minimize defects and optimize the molding process.
3. Eco-Friendly Materials
With a growing emphasis on sustainability, plastic mold makers are incorporating biodegradable or recovered materials into their processes.
The Future of Plastic Mold Makers
The future of plastic mold makers is bright, propelled by innovation and an increasing demand for custom, efficient manufacturing solutions. Emerging fields, such as electric vehicles and sustainable consumer goods, offer exciting opportunities for mold makers. Adapting to changing market trends and technological advancements will be crucial for continued success.
Conclusion
In conclusion, plastic mold makers are the backbone of many industries, translating designs into functional products that shape our world. Their expertise, combined with technological advancements, is paving the way for a future filled with innovation and sustainable practices. Companies like Deep Mould at deepmould.net stand at the forefront of this dynamic field, offering exceptional solutions and quality service in the ever-evolving landscape of manufacturing.
As the market continues to grow and evolve, the significance of skilled plastic mold makers will only increase, highlighting the importance of quality craftsmanship in today’s manufacturing processes.