Automotive Mould: A Comprehensive Overview
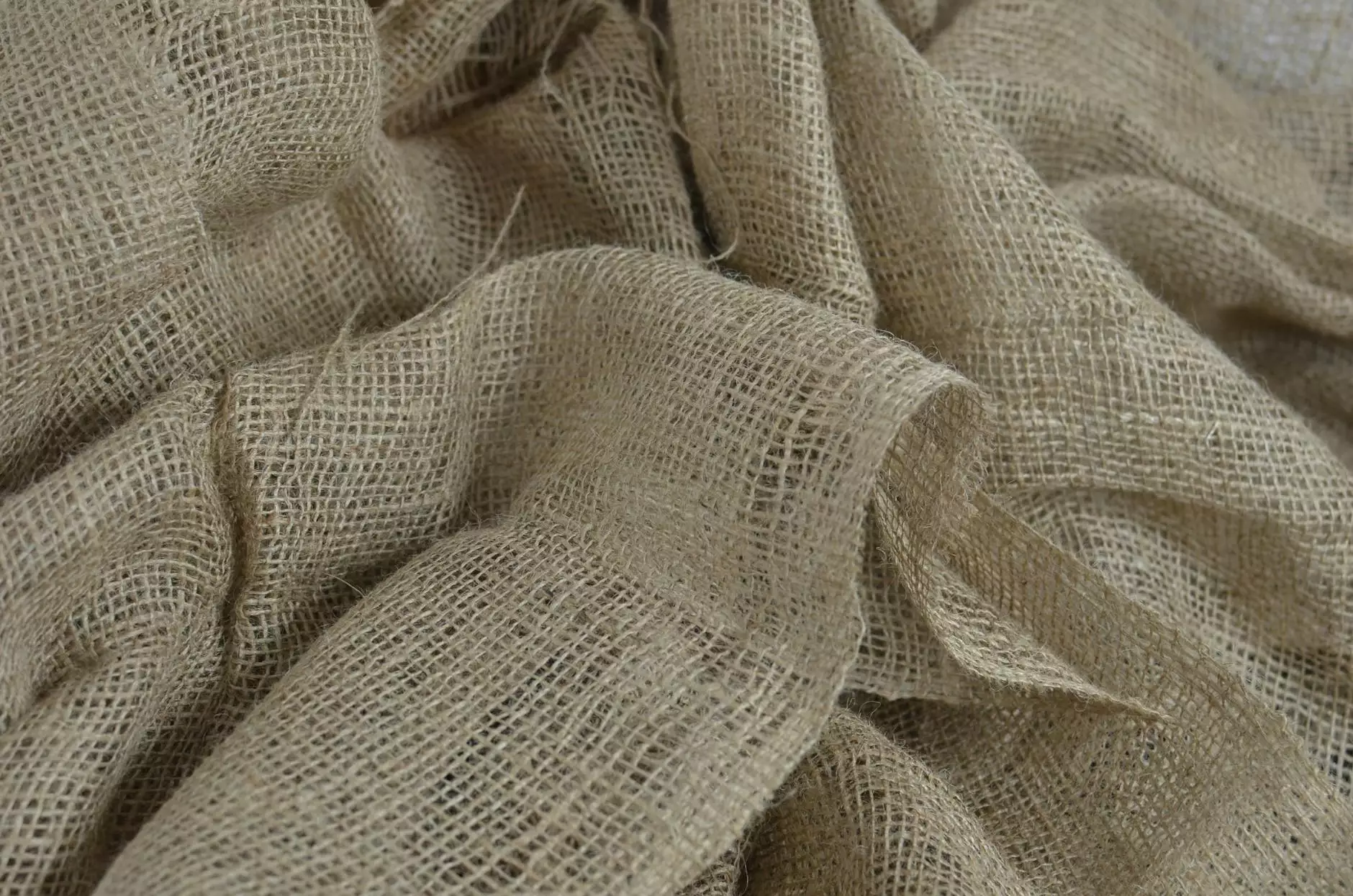
The realm of the automotive industry is a complex, ever-evolving landscape where precision, efficiency, and quality reign supreme. Automotive mould technology is at the forefront of this evolution, playing a crucial role in the production of vehicles and their components. This article delves deep into the world of automotive mould, the processes involved, and the pivotal role of companies like Deep Mould in ensuring that the highest standards of quality are met through expert metal fabrication.
Understanding Automotive Mould
At its core, automotive moulding refers to the process of shaping materials using moulds specifically designed for automotive applications. This process is integral to both the manufacturing of parts and the assembly of complete vehicles. The materials most commonly used in automotive moulding include various metals and plastics, making metal fabricators essential players in the automotive supply chain.
The Importance of Precision in Automotive Moulding
Precision is non-negotiable in any aspect of the automotive industry. A small deviation in the dimensions of a component can lead to malfunction or safety hazards. Therefore, automotive mould designs must be meticulously crafted. This precision ensures that each component fits perfectly within the intricate assembly of a vehicle, contributing to its overall performance, durability, and safety.
- Quality Control: Implementing stringent quality control measures at every stage of the moulding process is vital.
- Advanced Technology: Utilizing state-of-the-art technology in mould design and development enhances accuracy.
- Skilled Workforce: A skilled workforce trained in metal fabrication techniques is essential for maintaining high standards.
Types of Automotive Mould
There are several types of automotive moulds used in the industry, each designed for specific applications. Here, we’ll break down some of the most common types:
1. Injection Moulds
Injection moulds are widely used for creating plastic parts for vehicles. During this process, melted plastic is injected into a mould to form a specific shape. The benefits of injection moulding include:
- High precision and repeatability
- Ability to produce complex shapes
- Efficient manufacturing process
2. Compression Moulds
Compression moulding involves shaping materials by applying heat and pressure. This method is ideal for rubber and thermosetting polymers, making it suitable for gaskets and seals in automotive applications. The process is characterized by:
- Lower setup costs
- Versatility in material use
- Production of large parts
3. Blow Moulds
Blow moulding is primarily used for creating hollow parts, such as fuel tanks and other storage components. The process uses air pressure and is known for:
- Cost-effectiveness
- Ability to create lightweight structures
- High production speed
Key Benefits of Automotive Mould Technology
Automotive mould technology revolutionizes vehicle manufacturing by providing several key benefits:
Enhanced Production Efficiency
With state-of-the-art moulding techniques, manufacturers can produce high volumes of parts quickly and efficiently. This rapid production capability not only reduces manufacturing lead times but also helps in meeting the increasing demand in the automotive sector.
Improved Material Utilization
Modern automotive mould processes allow for better material utilization, minimizing waste and reducing overall production costs. This increased efficiency contributes to a more sustainable manufacturing process, which is crucial in today’s environmentally-conscious market.
Customization Capability
Custom automotive mould solutions enable manufacturers to create bespoke parts tailored to specific designs and requirements. This flexibility is essential for automotive companies looking to differentiate their products in a competitive marketplace.
The Role of Deep Mould in Automotive Moulding
As a leader in the field of metal fabrication, Deep Mould specializes in providing high-quality automotive mould solutions. With years of experience and a commitment to excellence, Deep Mould stands out from the competition. Here’s how:
Expertise in Metal Fabrication
Deep Mould employs a team of highly skilled professionals adept in the latest metal fabrication techniques. Their expertise enables them to create precision moulds that meet the stringent requirements of the automotive industry.
Investment in Technology
Staying ahead in the automotive mould industry requires continuous investment in technology. Deep Mould utilizes advanced CAD/CAM software and CNC machining technologies to create accurate and reliable moulds.
Commitment to Quality
Quality is the cornerstone of Deep Mould’s operations. Rigorous quality assurance processes are implemented at each stage of production, ensuring that all moulds deliver unparalleled performance.
Future Trends in Automotive Moulding Technology
The automotive industry is in a state of constant innovation. Here are some trends shaping the future of automotive moulding:
1. Lightweight Materials
The push for increased fuel efficiency and reduced emissions is driving the demand for lightweight materials in automotive manufacturing. Moulding processes are evolving to accommodate these new materials, enhancing performance while maintaining safety standards.
2. Automation and Robotics
Automation and robotics are becoming more prevalent in the moulding process. These technologies enhance precision, reduce human error, and improve overall manufacturing efficiency.
3. Eco-Friendly Practices
As sustainability becomes a priority for consumers and manufacturers alike, there is a growing emphasis on eco-friendly moulding practices, including recycling waste materials and utilizing biodegradable substances in manufacturing.
Conclusion: Driving Forward with Automotive Mould
In conclusion, automotive mould technology is a vital component of modern vehicle production. Its importance can’t be overstated, as it underpins the quality, safety, and efficiency of automotive components. Companies like Deep Mould are instrumental in this ecosystem, providing top-notch metal fabrication services that adhere to industry standards and client specifications.
As we look to the future, ongoing advancements in technology and shifts towards sustainable practices will continue to shape the landscape of automotive moulding. Manufacturers and consumers alike can look forward to innovative solutions that not only meet current needs but also pave the way for a greener, more efficient automotive industry.