Understanding the Industrial Location Model: A Guide for Architects
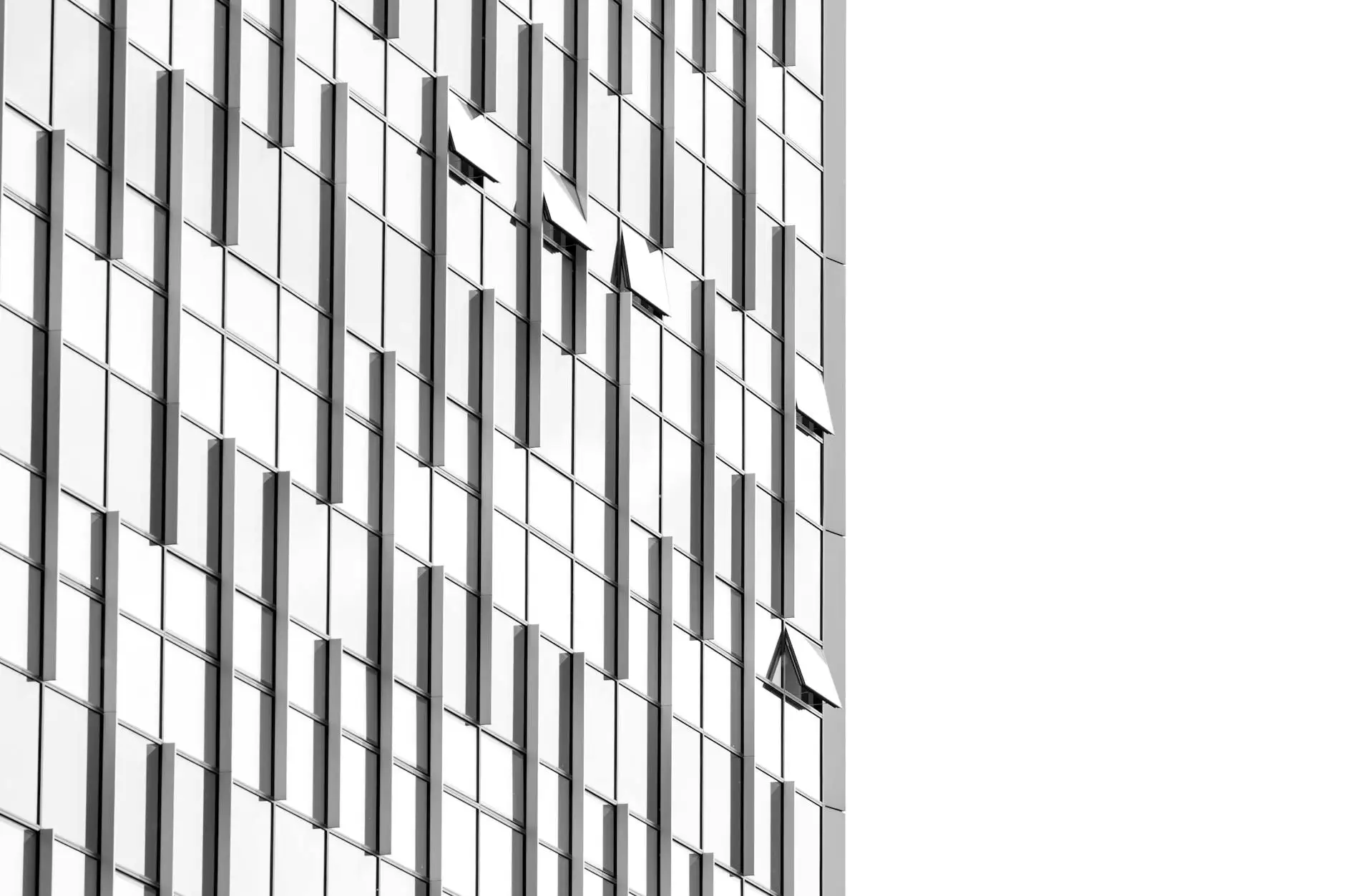
The Industrial Location Model is a pivotal concept within the field of urban planning and architecture. It provides architects and planners with a framework to evaluate and determine optimal site selection for industrial facilities. In this comprehensive article, we will delve into the key aspects of this model, its historical background, fundamental principles, and its practical applications within the realm of architecture.
What is the Industrial Location Model?
The Industrial Location Model refers to a theoretical framework that analyzes the geographic distribution of industrial activities. It serves as a tool for understanding how and why certain industries prefer specific locations. The underlying principles of this model are essential for architects involved in designing industrial structures, ensuring they are situated in locations that optimize operational efficiency, minimize costs, and maximize accessibility.
Historical Background of the Industrial Location Model
The origins of the Industrial Location Model can be traced back to early economic geographers such as Alfred Weber, who introduced the concept in his seminal work "Theory of the Location of Industries" in 1909. Weber's theory proposed that the location of an industrial plant is influenced by transportation costs, labor availability, and the costs attributed to raw materials. Understanding this historical context helps architects appreciate the evolution of industrial planning.
The Key Components of the Industrial Location Model
The Industrial Location Model is built upon several key components that affect the decisions surrounding industrial site selection:
- Transport Costs: The proximity to raw materials and markets is critical. A site that minimizes transportation costs will enhance profitability.
- Labor Availability: The availability of a skilled workforce impacts the choice of location. Areas with high unemployment rates may provide a larger labor pool.
- Raw Material Accessibility: Industries that rely heavily on particular raw materials tend to be located near their sources, reducing shipping costs.
- Market Access: Proximity to markets can dictate the success of an industrial venture, making market accessibility a crucial factor.
- Government Policies: Local zoning laws, tax incentives, and government support can influence industrial location decisions.
Practical Applications of the Industrial Location Model in Architecture
Understanding the Industrial Location Model is invaluable for architects as it informs various practical aspects of site selection and building design.
Site Selection
When architects engage in the planning phases of industrial projects, they utilize the Industrial Location Model to carefully evaluate potential sites. Key considerations include geographical advantages, access to transportation networks, and synergies with existing infrastructures.
Design Considerations
The insights gained from the Industrial Location Model can significantly inform the design of industrial facilities. For instance, architects must account for:
- Space Requirements: Understanding the industrial process can dictate the necessary space allocation.
- Workflow Efficiency: The design must facilitate smooth workflows, incorporating natural movement paths for materials and personnel.
- Flexibility in Design: Given the rapid changes in technology and market conditions, architectural plans should allow for future expansions or scalability.
Environmental Impact
Incorporating the Industrial Location Model also encourages sustainability. Architects can plan industrial sites that minimize environmental footprints by considering factors such as local ecosystems, waste management systems, and resource conservation.
Challenges in Implementing the Industrial Location Model
While the Industrial Location Model provides a structured approach to site selection, architects must navigate several challenges:
- Dynamic Economic Conditions: Changes in the economy can rapidly alter transportation costs, labor markets, and material availability.
- Regulatory Hurdles: Navigating through local regulations can complicate site selection, impacting project timelines.
- Technological Advancements: The emergence of new technologies can disrupt traditional industrial processes and, consequently, location advantages.
The Future of the Industrial Location Model
As global industries evolve, so too must the Industrial Location Model. The rise of e-commerce, automation, and smart factories necessitates a reevaluation of traditional location principles. Architects and planners are tasked with adapting to these changes, ensuring facilities are not only strategically located but also equipped with advanced technologies.
Integration of Smart Technologies
The future of industrial architecture will likely see greater integration of smart technologies. Automated systems and IoT (Internet of Things) applications can optimize resource distribution and workplace efficiency. The Industrial Location Model will need to consider how digital infrastructure complements traditional factors in site selection.
Focus on Sustainability
Future applications of the Industrial Location Model will increasingly emphasize sustainability. As environmental regulations become stricter and public opinion shifts towards greener practices, architects must prioritize sustainability in their designs. This includes:
- Utilizing renewable energy sources.
- Incorporating efficient waste management solutions.
- Designing buildings with a lower carbon footprint.
Conclusion
In conclusion, the Industrial Location Model is an indispensable tool for architects and urban planners alike. Its comprehensive approach to site selection intertwines economic factors, labor considerations, and market access while accounting for modern technological advancements and sustainability. As industries continue to evolve, a nuanced understanding of this model will empower architects to create efficient, strategic, and environmentally conscious industrial facilities that meet the needs of the future.